The humanoid robotics revolution is just around the corner. Test models are already working in factories alongside human beings across the world, while AI companies develop new foundation models designed to help robots navigate their environments as easily as humans do.
But computer “brains” are useless without the skeletons that give humanoid robots their form—and the many components that make up those skeletons need to come from somewhere. Alongside bearings, which reduce friction, motors, and gears, the average humanoid robot relies on dozens of screws—key components that convert the rotational motion produced by a motor into linear motion.
Traditionally, ball screws—which feed a series of balls through a screw shaft and nut—have been the primary type used in robotics. But a new component is set to supercharge humanoid motion and could become the next must-have physical part. “Over time, planetary roller screws should represent the majority of screws used in humanoids,” researchers at Morgan Stanley wrote in a February 2025 note.
Planetary roller screws are a next-generation alternative to ball screws, able to withstand higher loads and last longer—both vital qualities for the wear and tear humanoid robots are expected to endure over their operational lifetimes. Tesla’s Optimus uses four planetary roller screws in its calves, and they’re also used by Figure AI, Agility, 1X, and the majority of China’s humanoid robot manufacturers. One China-based expert, Jack Li, research and development and product manager at Nanjing Process Equipment, a Chinese screw manufacturer, told investment bank Jefferies that the total market for the screw is already $1.8 billion, and is likely to grow at a compound rate of more than 30% over the next five years.
Actuators—described as “the crown jewel of the core moving parts of robots”—convert rotary motion into linear motion, a crucial function for robotics and especially for humanoid robots, says Jonathan Aitken, an expert in robotics at the University of Sheffield. “They’re highly accurate as we get good precision in conversion from angle to linear distance travelled,” he explains. “Traditionally linear actuation isn’t good for load, rotational is. This gives the best of both.”
So far, the use of planetary roller screws in humanoids has been limited by their cost—a result of the specialist skills needed to manufacture them reliably, which only a handful of companies worldwide currently possess. “The bulk of the cost of a humanoid will be in the actuators,” says Scott Walter, widely considered one of the world’s leading experts on robot design. Walter is chief technical advisor for Visual Components, a manufacturing production design company. “Each bot needs 40 or more,” he says. “So that is a huge supply need.”
Researchers at J.P. Morgan estimate that reducers and roller screws account for around 33% of the average humanoid robot’s “bill of materials,” or cost of parts. The average planetary roller screw sells for between $1,350 and $2,700, according to the investment bank. While Walter admits, “The logical choice would be just to use rotary actuators at all the joints, since the actuators axle can also form the joint,” cost concerns are currently holding back their widespread deployment.
That looks set to change as engineering and manufacturing expertise grows alongside demand, driving down production costs. China appears to be in the driving seat when it comes to controlling the supply of planetary roller screws in the years ahead. “Because of drone manufacturing, China already had a large installed base of small actuator manufacturers,” says Walter. “While not having exactly the same requirements, they were close enough to allow China to produce enough rotary actuators at scale for initial bot prototypes,” he says. “They are in the drivers’ seat if rotary rules the day.” Chinese companies are betting on the potential of planetary roller screws to meet future humanoid demand: In October 2024, Shanghai Beite Technology—traditionally a manufacturer of auto parts—announced a 1.85 billion yuan ($260 million) investment to build a facility dedicated to the production of planetary roller screws.
The West will likely need to compete by developing its own planetary roller screw supply chain—and fast—given the potential impact of increasing U.S. tariffs and the ongoing trade war with China, where most of these components are made. “The dirty little secret is even if actuators are assembled stateside, the important components are still coming from China because few companies have the expertise and equipment to produce vital components outside of China,” says Walter. “Planetary roller screws are precision equipment. For humanoids, they need to be small and efficient,” he adds.
Yet there’s a complication. “The supply chain does not yet exist because the designs are not yet locked,” Walter explains. “Nor is there a consensus on the size of this supply chain.” But quick action may be required if the humanoid robotics revolution turns out to be even a fraction of the size some experts predict.
Войдите, чтобы добавить комментарий
Другие сообщения в этой группе
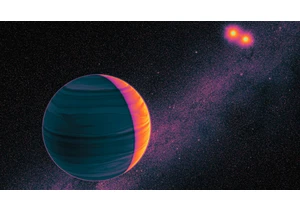
Child psychologists tell us that around the age of five or six, children begin to seriously contemplate the world around them. It’s a glorious moment every parent recognizes—when young minds start

During January’s unprecedented wildfires in Los Angeles, Watch Duty—a digital platform providing real-time fire data—became the go-to app for tracking the unfolding disaster and is credit

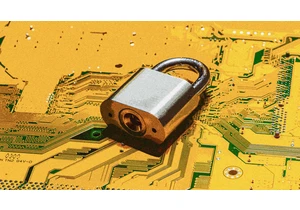
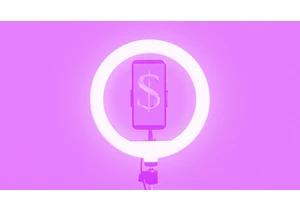
Yahoo’s bet on creator-led content appears to be paying off. Yahoo Creators, the media company’s publishing platform for creators, had its most lucrative month yet in June.
Launched in M

From being the face of memestock mania to going viral for inadvertently stapling the screens of brand-new video game consoles, GameStop is no stranger to infamy.
Last month, during the m
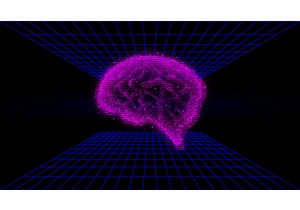
The technology industry has always adored its improbably audacious goals and their associated buzzwords. Meta CEO Mark Zuckerberg is among the most enamored. After all, the name “Meta” is the resi