When a wind turbine reaches the end of its life after two or three decades, the giant blades attached to it usually end up in a landfill.
That’s largely because of the materials that are used. “[The blade is] a sandwich of different materials that are all tied together with glue,” says Tom Siekmann, CEO of Voodin Blades, a Germany-based startup that recently designed a wooden version that could replace typical blades. “And even though it might be possible to recycle each component of that sandwich individually, it’s really difficult to take them apart and recycle them.” It’s even harder because blades can be longer than a football field and cumbersome to move.
The recycling process is so expensive that it typically doesn’t happen. If it does, the blades are downcycled into lower-quality products, like cement.
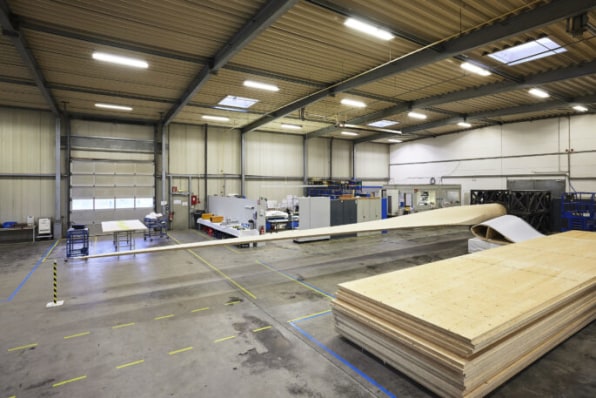
A couple of years ago, Siekmann was having drinks with friends who worked in the wind power industry, and the conversation turned to the problem. “We thought, Okay, what else can we do? What’s a more sustainable, easier-to-recycle material?” They started to consider wood. After some initial calculations showed that the design might be viable, they built small samples and then a prototype.
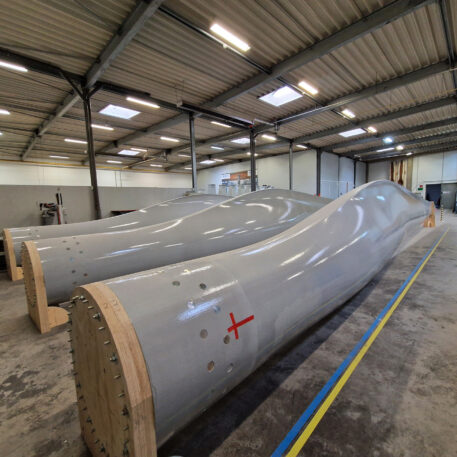
Voodin Blades uses high-tech laminated lumber, a very strong material that has similar characteristics to glass fiber, held together by a glue designed to work with wood. The startup, which was part of the latest cohort at a sustainable design accelerator called Circular Valley, is thinking carefully about how the material can avoid landfills.
If a wind turbine using the new wooden blades is dismantled, the blades can be reused or repurposed for construction or other products. If they aren’t reused, they can also be burned; the process is carbon neutral, since the wood contains CO2 that was recently captured from the atmosphere by trees. If for some reason they’re thrown out, they’re biodegradable.
Because the manufacturing process uses far less energy than making a typical blade, and because it avoids components made from fossil fuels, the carbon footprint of production is 78% smaller. The design also enables more automation in manufacturing, so the company expects it to be 20% cheaper to produce than standard blades.
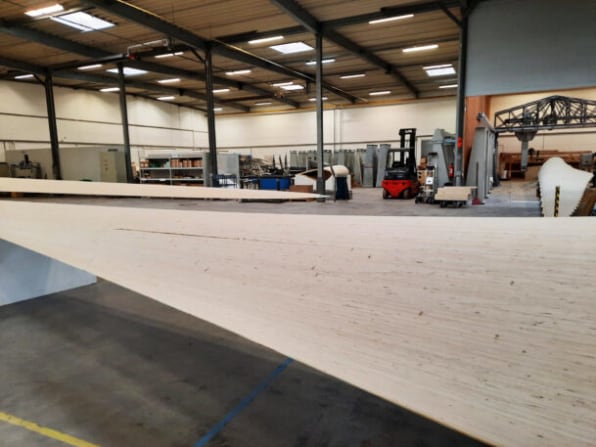
The company recently manufactured a prototype that will be tested on a small wind turbine after getting regulatory approval. It will also soon begin working with a wind turbine manufacturer to design much larger custom blades for state-of-the-art turbines.
Wind turbine manufacturers have known about the end-of-life problem for years, but because a turbine might last 35 years, they waited to address it. Now it’s becoming more urgent. Globally, as many as 14,000 blades may be decommissioned each year over the next few years, and that number will grow. By 2050, it could add up to 43 million metric tons of waste.
Ak chcete pridať komentár, prihláste sa
Ostatné príspevky v tejto skupine

Tokenization has long been a buzzword for crypto enthusiasts, who have been arguing for years that blo
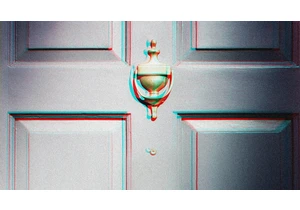
Ding dong ditching has resurfaced as the “door kick challenge.” But this time it could lead to criminal charges and potentially deadly consequences.
In Florida this week, five mino

Alphabet beat Wall Street estimates for its second quarter on Wednesday, and cited massive
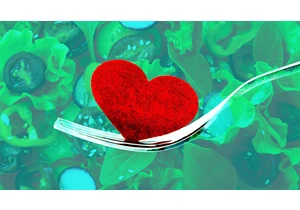
It’s been said that online dating killed the meet cute. Now, as people struggle with dating app burnout, some are supposedly resorting to stealing men’s lunches for a chance at creating their own.

An artificial intelligence agenda that started coalescing on the podcasts of

Tesla is likely to post its

A Trenta Starbucks is no longer cutting it. The latest coffee trend has people ordering their iced lattes by the bucket.
Earlier this year, independent coffee shops started going viral